Mastering Injection Mold Tool Design for Optimal Business Performance
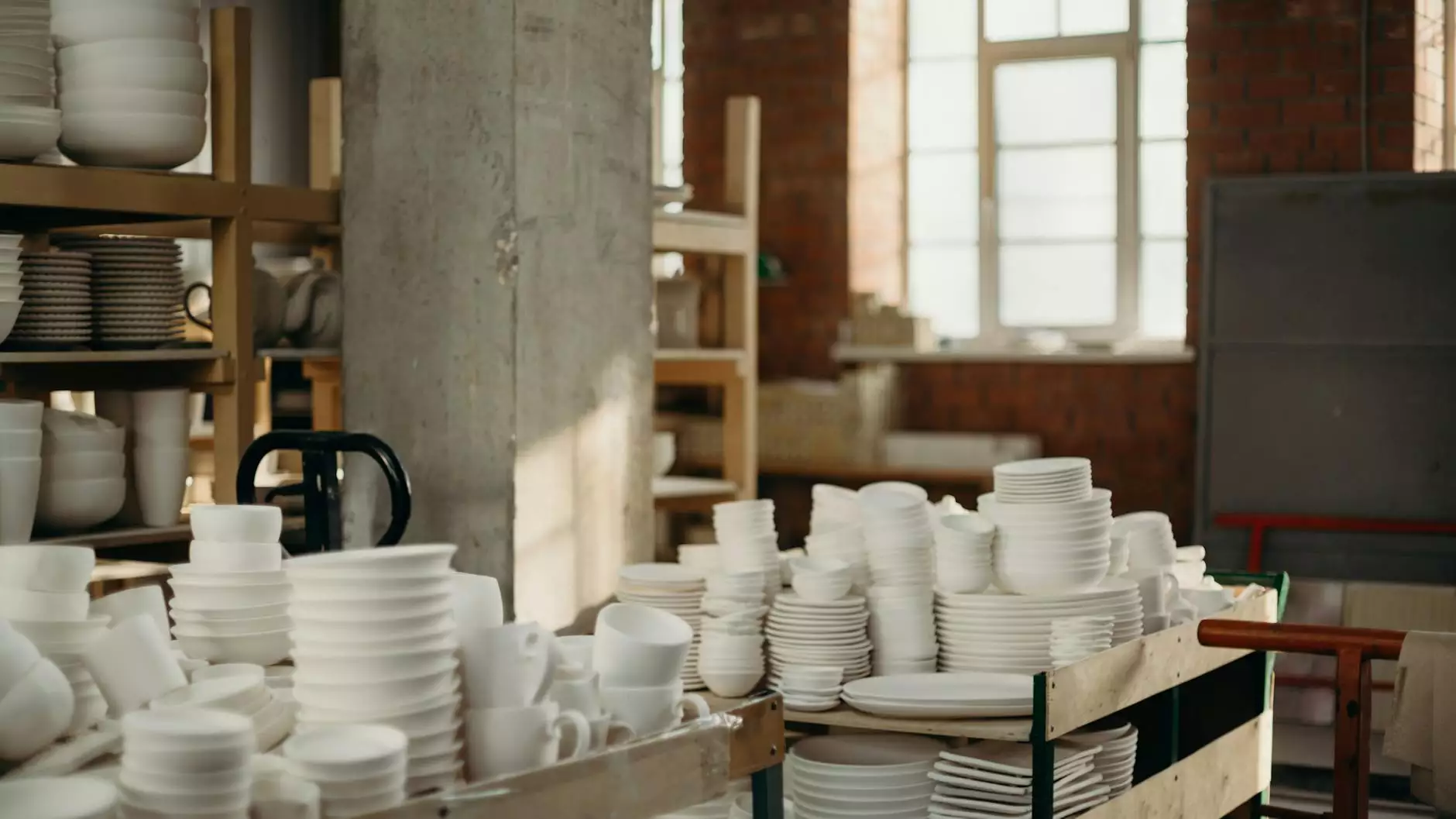
In the competitive landscape of metal fabrication, having the right manufacturing techniques can spell the difference between success and failure. One essential aspect that greatly influences manufacturing efficiency and product quality is injection mold tool design. This article delves into the intricacies of injection mold tool design, its importance, benefits, and how it can significantly enhance your business operations at deepmould.net.
The Essential Role of Injection Mold Tool Design
Injection mold tool design is at the very heart of the plastic injection molding process. It involves creating and refining molds that allow for the precise shaping of molten plastic into finished products. The design quality of these molds can determine the efficiency, cost-effectiveness, and longevity of the manufacturing process.
1. Understanding Injection Molding
Before delving into the specifics of mold design, it is crucial to understand what injection molding entails. This method involves the following steps:
- Heating: Plastic pellets are heated until they become molten.
- Injecting: The molten plastic is injected into the mold at high pressure.
- Cooling: The plastic is allowed to cool and solidify inside the mold.
- Removing: The finished part is extracted from the mold once cooled.
The entire process is highly dependent on the quality and precision of the molds designed. Therefore, investing in the best injection mold tool design is crucial for any business in the metal fabrication sector.
Key Advantages of Superior Injection Mold Tool Design
The advantages of well-executed injection mold tool design are manifold:
- Increased Production Efficiency: A well-designed mold can facilitate faster production cycles, reducing lead times.
- Enhanced Product Quality: Precision in design ensures uniformity and reduces defects, leading to higher customer satisfaction.
- Cost Reduction: Effective mold design minimizes material waste and downtime, significantly decreasing operational costs.
- Longer Mold Life: High-quality materials and design reduce wear and tear, prolonging the life of the mold.
- Flexibility and Versatility: Great design accommodates various plastics and modifications, allowing businesses to adapt quickly to market demands.
2. Components of Effective Injection Mold Tool Design
To achieve optimal results, several components must be considered in the injection mold tool design process:
2.1 Mold Layout
The layout of the mold is critical. It must maximize the available space while ensuring the efficiency of the injection process. Factors to consider include:
- Thermal expansion and contraction of materials.
- Flow path efficiency to reduce cycle time.
2.2 Cooling System Design
Effective cooling systems are vital for maintaining the quality of the injected product. The cooling channels should be strategically placed to allow consistent temperature throughout the mold, leading to improved solidification and reduced cycle time.
2.3 Ejection Mechanism
The ejection system must be designed to remove the finished product from the mold without damaging it. Different systems include:
- Mechanical ejection.
- Pneumatic systems.
- Hydraulic ejectors.
2.4 Material Selection
The choice of material for the mold affects durability and performance. Common materials include:
- Steel alloys for long life and durability.
- Aluminum for lower-cost molds used for prototype designs.
3. Modern Innovations in Injection Mold Tool Design
The field of injection mold tool design has seen remarkable advancements in recent years. These innovations not only enhance efficiency but also improve the overall quality of production:
3.1 3D Printing Technology
3D printing has revolutionized the design process by allowing for rapid prototyping and testing of molds before full-scale production, enabling businesses to iterate designs and solve problems at a faster pace than ever before.
3.2 Computer-Aided Design (CAD)
CAD software allows for precise visualization and modification of mold designs. This technology helps in simulating the injection process to predict potential issues such as air traps or cooling problems before the physical mold is created.
3.3 Advanced Simulation Software
Utilizing simulation software can provide insights into flow dynamics, temperature distributions, and potential defects. These predictive tools enable engineers to optimize designs thoroughly before manufacturing begins.
4. Best Practices in Injection Mold Tool Design
To maximize the effectiveness of your injection mold tool design, consider implementing the following best practices:
4.1 Collaborate with Design Experts
Work alongside skilled designers and engineers who specialize in injection mold tool design. Their expertise can guide you through complex decisions and innovative techniques.
4.2 Regularly Review and Update Designs
Market demands and materials are continually evolving. Regular audits of your mold designs can ensure your business stays ahead of the competition.
4.3 Focus on Continuous Improvement
Encourage a culture of continuous improvement within your organization. Implementing feedback loops from production can highlight areas for mold enhancement.
Conclusion: Transform Your Business with Injection Mold Tool Design
In conclusion, focusing on injection mold tool design is essential for any business striving for success in the metal fabrication industry. By investing in high-quality designs, employing modern innovations, and adhering to best practices, you can dramatically enhance your operational efficiency and product quality. At deepmould.net, we pride ourselves on our expertise in creating superior mold designs that drive business growth. Don’t underestimate the power of a well-designed injection mold; it's a critical component that can shape the future of your business.
Contact Us
If you are interested in learning more about how injection mold tool design can benefit your operations, please reach out to us on our website: deepmould.net. Our team of experts is ready to assist you in enhancing your manufacturing processes!