Understanding Oil Seal Manufacturing in the Diesel Engine Parts Industry
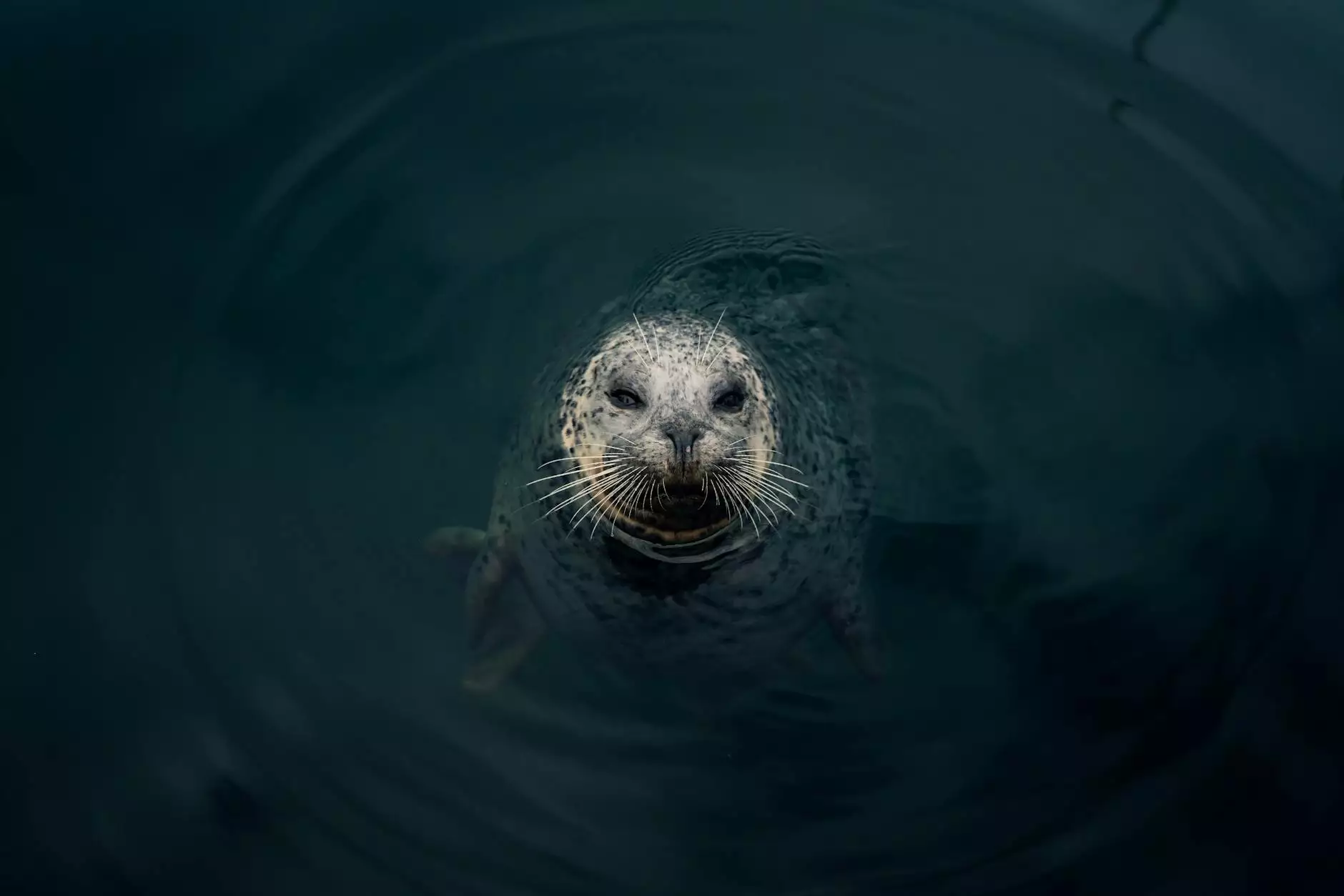
In the world of mechanical engineering, particularly within the realm of diesel engine parts, the significance of oil seal manufacturing cannot be overstated. Oil seals play a pivotal role in sealing systems, preventing the leakage of fluids within machinery and contributing to overall operational efficiency. This article delves into the complexities of oil seal manufacturing, exploring its importance to diesel engine components, and detailing how it aligns with the needs of spare parts suppliers.
The Role of Oil Seals in Diesel Engines
Oil seals, also referred to as grease seals, are designed to protect bearings and moving parts in diesel engines from external contaminants. In a diesel engine, these seals are crucial for multiple reasons:
- Fluid Retention: Oil seals prevent lubricants from leaking out, maintaining the necessary lubrication for engine components.
- Dirt and Contaminant Protection: They act as barriers against dust, dirt, and other contaminants that could cause wear and tear on engine components.
- Improved Performance: By ensuring that the lubricants stay where they are needed, oil seals contribute to better overall engine performance and longevity.
Key Materials in Oil Seal Manufacturing
The manufacturing process of oil seals involves selecting the right materials that can withstand high pressures, temperatures, and various chemical exposures. Common materials used in oil seal manufacturing include:
- Nitrile Rubber (NBR): Known for its excellent resistance to temperature and oil, this is the most commonly used material for oil seals.
- Fluoroelastomer (FKM): This material is ideal for high-temperature applications and provides strong chemical resistance.
- Polyurethane: It offers high wear resistance and has excellent sealing properties, making it suitable for various industrial applications.
Processes Involved in Oil Seal Manufacturing
The process of manufacturing oil seals is intricate and requires precision to ensure quality and durability. Here’s a brief overview of the standard processes involved in oil seal manufacturing:
1. Design and Prototyping
The first step in oil seal manufacturing is creating a precise design that meets specific operational requirements. Advanced software tools are utilized for this purpose.
2. Material Selection
Once the design is finalized, the next step involves selecting the appropriate materials based on the application and environmental factors.
3. Molding
The selected material is then processed using techniques such as molding or extrusion to create the seal’s shape. This stage plays a crucial role in establishing the seal’s integrity.
4. Quality Control
Post-manufacturing, each oil seal undergoes rigorous quality control checks to ensure it meets specified parameters and standards. This typically involves stress testing and performance validation.
5. Packaging and Distribution
Finally, once the oil seals have passed all quality checks, they are packaged and prepared for distribution to clients and spare parts suppliers.
Importance of Quality in Oil Seal Manufacturing
Quality assurance in oil seal manufacturing is critical. High-quality seals contribute to:
- Reliability: Ensuring that equipment functions properly over an extended time.
- Cost Efficiency: Reducing maintenance costs associated with leaks and repairs.
- Safety: Preventing accidents that can occur due to lubricant leaks.
Oil Seal Manufacturing: The Impact on Spare Parts Suppliers
For spare parts suppliers, the connectivity with reliable oil seal manufacturers is paramount. A consistent supply of high-quality seals facilitates:
- Supply Chain Efficiency: Streamlined processes that ensure timely availability of parts.
- Customer Satisfaction: Meeting the demands of clients with top-tier products enhances supplier reputation.
- Market Competitiveness: Suppliers that offer quality oil seals can differentiate themselves in a crowded market.
Future Trends in Oil Seal Manufacturing
As industries evolve, so do the methods of oil seal manufacturing. Some emerging trends include:
- Innovative Materials: Continuous research into new polymers and composites to enhance performance.
- Sustainability: Increased focus on environmentally friendly processes and materials.
- Smart Technology: Integration of IoT technology to monitor seal performance in real-time.
Conclusion
The intricate field of oil seal manufacturing is foundational to the functionality of diesel engines and the broader machinery landscape. By understanding the processes, materials, and importance of quality in oil seal production, businesses within the diesel engine parts sector can enhance their performance and reliability. As the industry evolves, staying ahead of trends and maintaining high standards will be crucial for manufacturers and suppliers alike.
At client-diesel.com, we prioritize superior quality in our diesel engine parts, including oil seals, ensuring that our customers receive only the best.